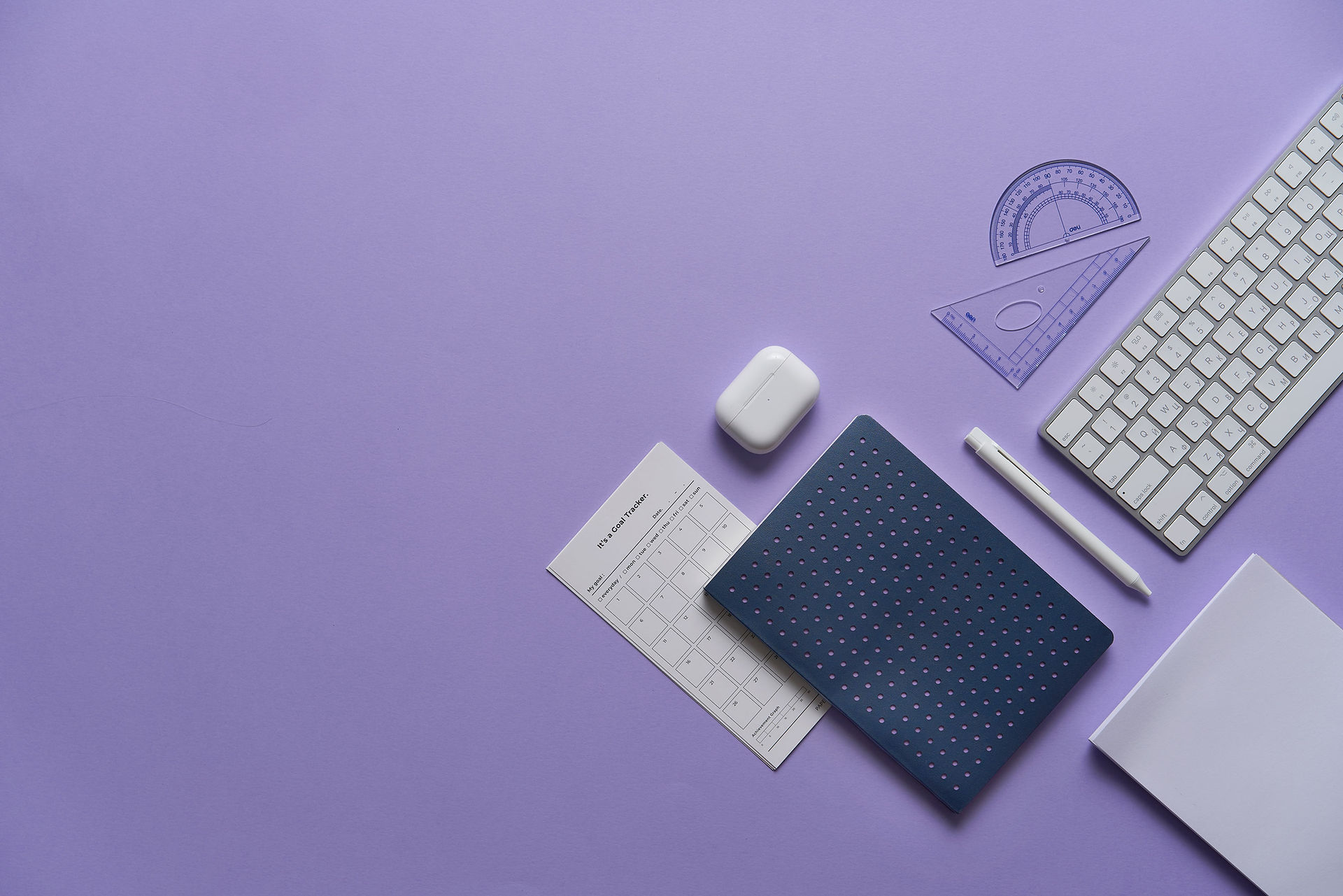
THE ORIGIN
Our main motive was to create a sustainable, eco-friendly, portable transportation device that would be easy to carry when not driving, for maximum theft protection. This device goes hand in hand with the current scenario of COVID-19 as the device is designed to carry only a single person, ensuring social distancing.

This page is dedicated to the origination of the "hows" and "whys" of this urban mobility vehicle.
INITIAL DESIGN
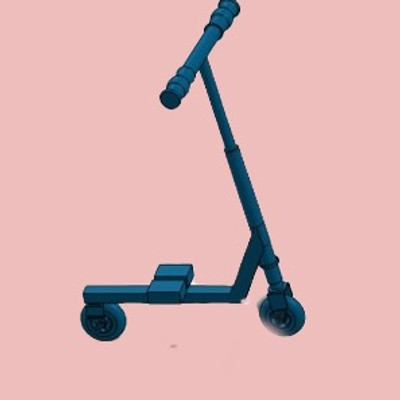
These designs were modeled to get a rough idea of how the final product could be like.
SELECTING THE POWER SOURCE

Weighted Matrix to select the power source
Points Allocation


Power Source Selected = Electric
PROSPECTIVE DESIGN IDEAS
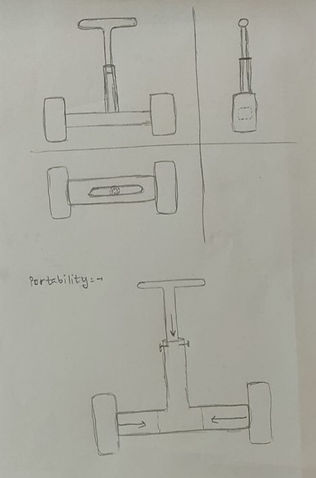
DESIGN SKETCH 1



DESIGN SKETCH 2

DESIGN SKETCH 3

DESIGN SKETCH 4
WEIGHTED MATRIX FOR DESIGN SKETCHES
Key information regarding the matrix
As the number of folds increases, the ease of foldability decreases.
In an educational campus method of carrying via trolley is much better than backpack, hence trolley=2 and backpack =1

Points Allocation

DESIGN-2 Selected
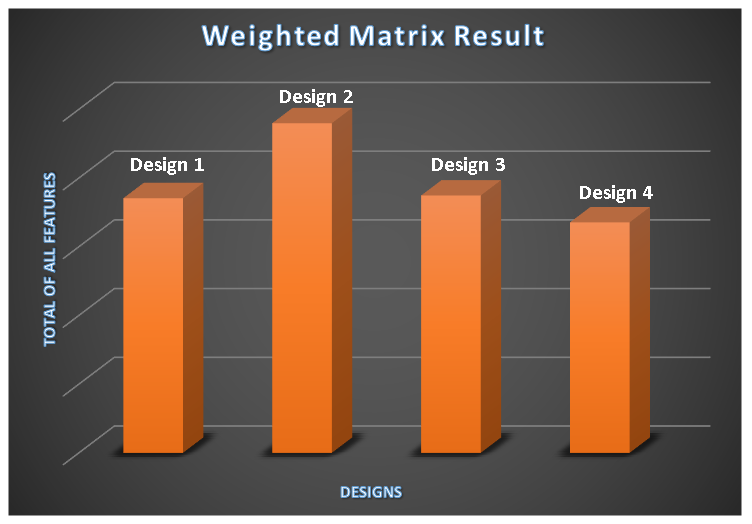
DIFFERENT DESIGNS OF FOOT-PAD

Design 1 & its Analysis

Design 2 & its Analysis

Design 3 & its Analysis
RESULT: Foot-pad design 2 is selected, as it has the minimum stress amongst the three designs
FIRST CAD MODEL BASED ON PRELIMINARY CALCULATIONS
FIRST BASIC MODEL
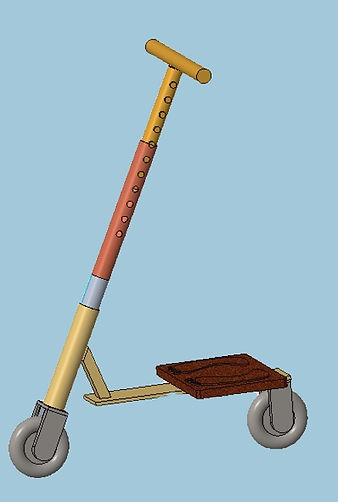

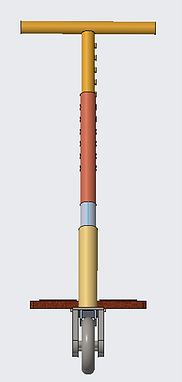
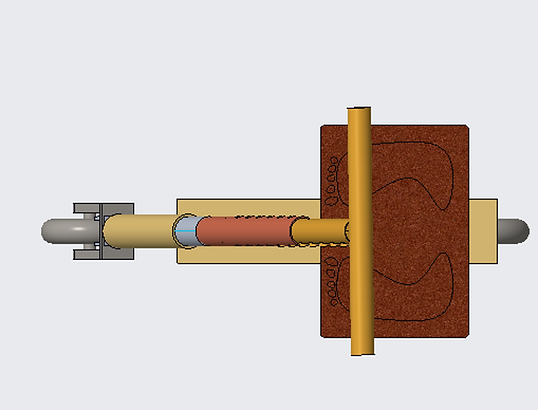
ITERATIONS IN DEVICE'S HANDLE



ADJUSTABLE HANDLE LENGTH
User can easily adjust handle height according to their convenience.
FIRST ITERATION IN DEVICE'S HANDLE

In this iteration, the handle length variability is retained from initial design, but due to handle being too long it can't be folded.
FINAL ITERATION IN DEVICE'S HANDLE


COMPLETELY FOLDABLE HANDLES
In this final iteration, the handle can be easily folded when the user is not using it.
ITERATION FOR BASE

Maximum Principal Stress is 33.46 MPa
Maximum Von Mises Stress is 42.24 MPa


Initial Base Design

Final Base Design
WEIGHTED MATRIX TO CHOSE MATERIAL (RESULT)
FEATURES CONSIDERED:
1.
Density (1000 Kg/m3)
2.
Young's Modulus (GPa)
3.
Cost (Rupees per Kgs)
4.
Hardness (Brinell)
5.
Yield Strength (MPa)
6.
Designer's Consideration

Weighted Matrix Result: If drilling is not required for the part.
Weighted Matrix Result: If drilling is required for the part.

WEIGHTED MATRIX TO CHOSE POWER SOURCE (RESULT)
FEATURES CONSIDERED:
1.
Distance travelled in 10 Rupees
2.
Weight of the power source (kgs)
3.
Average speed (kms/hr)
4.
Noise Produced (dB)
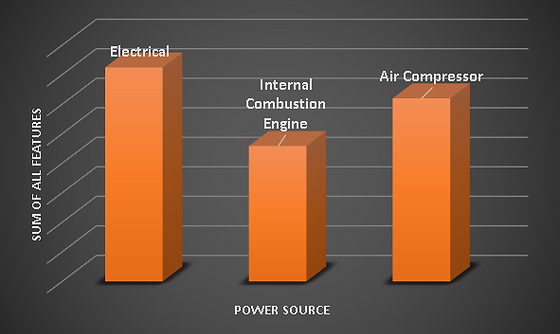
Weighted Matrix Result shows that Electrical power source should be chosen based on the above-consided factors.
ITERATION FOR BACK WHEEL

Added a pulley motor mechanism
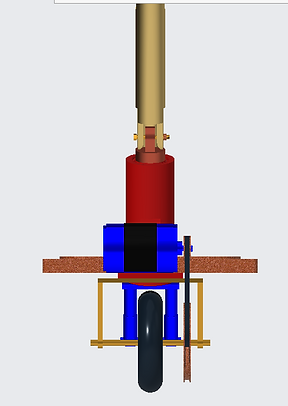
Implementing a pulley motor mechanism was a better a choice than regular chain motor mechanism giving the user a smoother, jerk-free ride.

FINALLY ADDED A HUB MOTOR, AS THE PULLEY MOTOR MECHANISM CONTRIBUTED TOO MUCH TO WEIGHT
For more details check out our final product gallery or click the red button way up top